In the first part of the history of CNC machines, we saw the evolutionary path of machine tools, from their birth to the introduction of the first numerical control systems, crossing the milestones that made it possible.
In this second appointment, we want to highlight the last step that gave birth to today’s CNC machine tools. To do this, we will look in detail at two events: the introduction of computers and the birth of drawing and design software. These two elements are now indispensable in the machines used in industrial production.
Integration of computers into machines
Until the 1950s, machine tools still used the punched card method. This system, although optimised, was still limited. The turning point came when this system was replaced by computers, marking the definitive transition from numerical control to modern CNC.
The first analytical engine dates back to 1800, but the first modern computer was realised at MIT. This prototype was capable of performing parallel calculations and using a magnetic core memory. Mass production began shortly afterwards. However, these prototypes were large in size, making application in many areas difficult.
In the 1960s, there was a change with the introduction of the first microcomputers onto the market. They were smaller and had a lower price than their predecessors, which made it possible for the first time to introduce new technologies into machines. Already from the first prototypes, it was evident the enormous potential this revolution could bring in terms of precision and the quantity of products that could be produced.
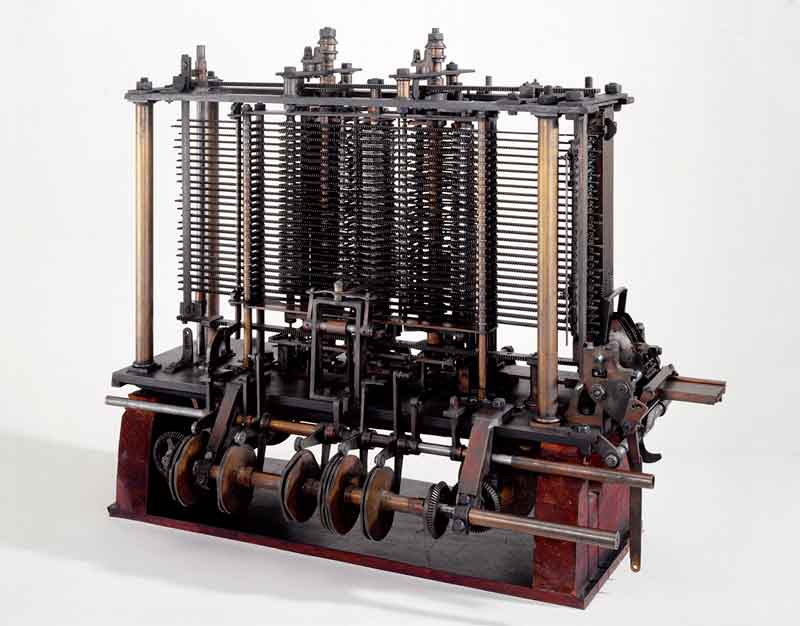
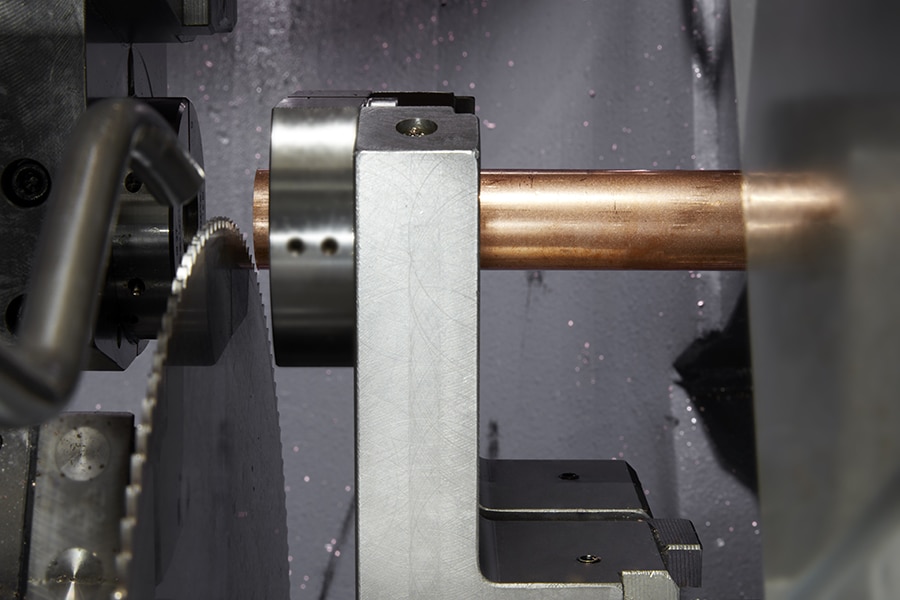
However, it took a few years before machine tools integrated with computer technology were seen as a competitive asset. In fact, a few years after their introduction, there was a period of slow economic growth and rising labour costs, which prompted companies to find cheaper ways to produce. Thus, machine tools began to be seen as a cheaper and more efficient solution than classical production methods.
The last big push for the introduction of CNC machine tools came with the market penetration of microprocessors and the strengthening of the LAN (Local Area Network) connection system in the 1980s. These elements made it less costly to use this type of machinery in manufacturing plants.
The birth of CAD and CAM software
CNC machines have benefited greatly from the rapid development that computer technology has had since the last decades of the last century. However, there were not only improvements in computers, but also in the software applicable to them, such as drawing and programming software.
There are two main programmes of this type that act as intermediaries between the computer and the CNC machines: computer-aided design (CAD) and computer-aided manufacturing (CAM). CAD can digitally create a 2D or 3D object, modify it and share it with other users. While CAM allows the user to select the tool, material and other variables to programme the actions to be performed by the machine.
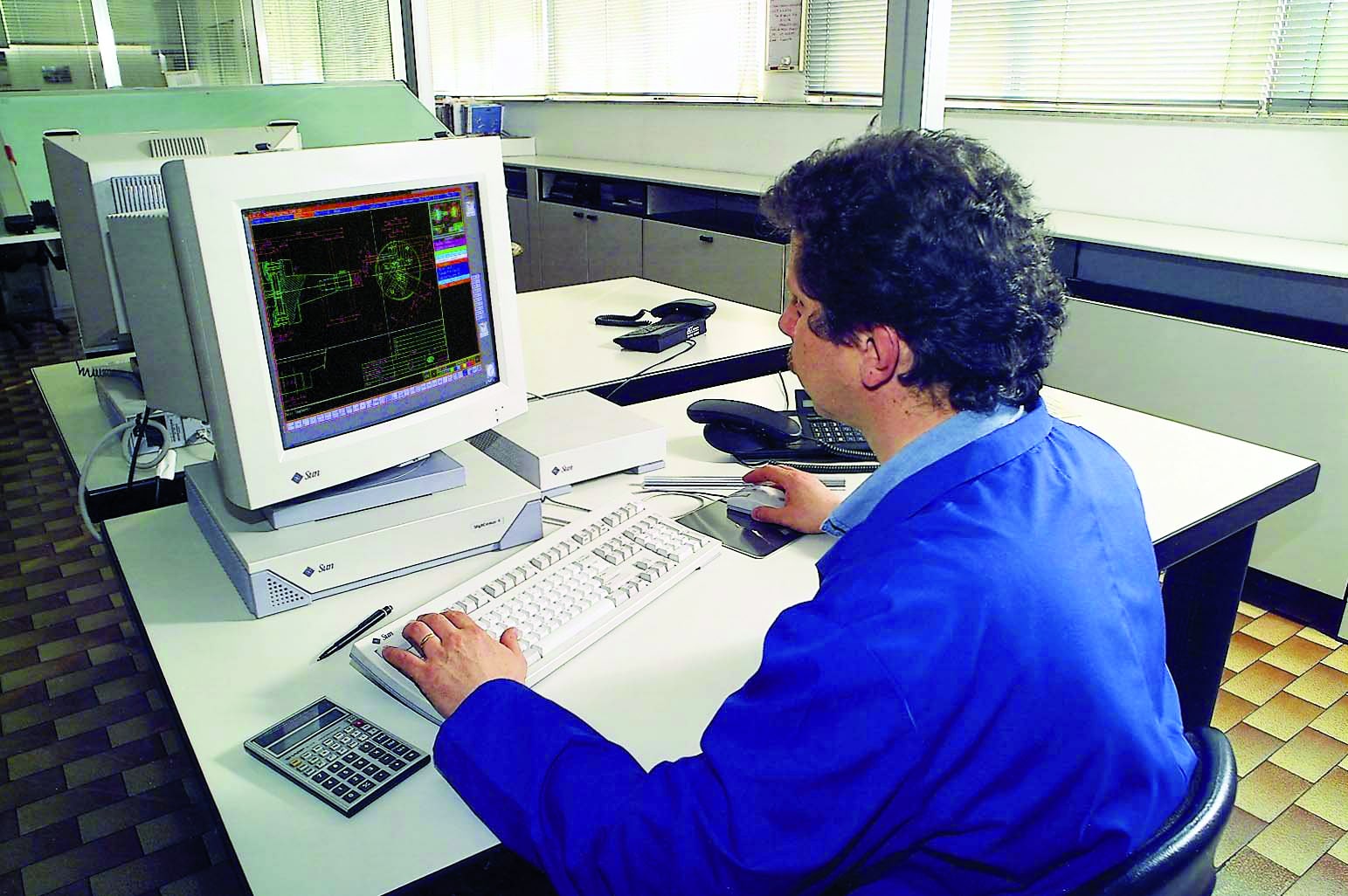
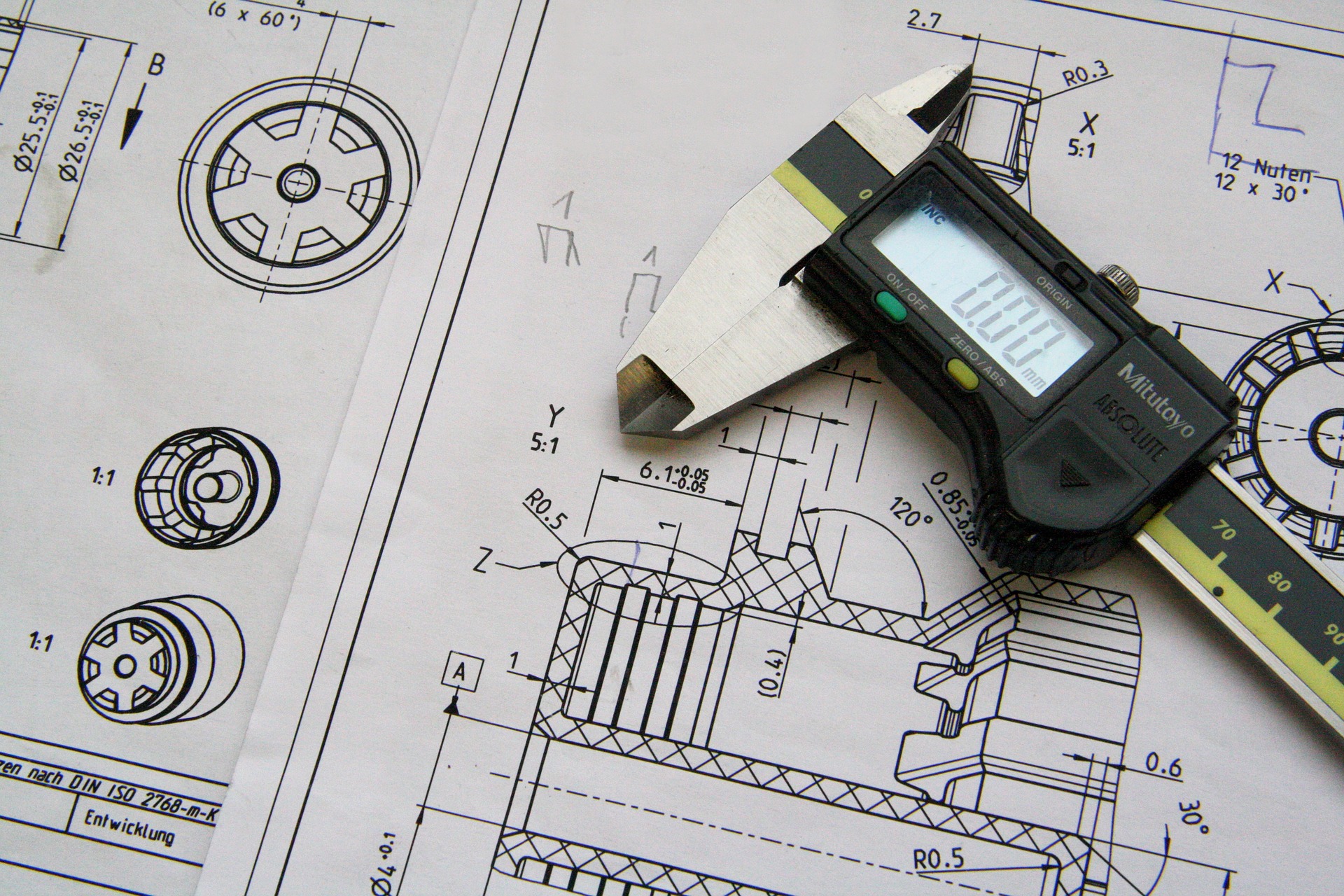
The universally recognised father of CAD and CAM systems is the scientist Patrick J. Hanratty. In a General Motors research laboratory, he developed a system for digital drawing, Design Automated by Computer (DAC), and shortly afterwards also the Pronto programme, a tool for numerical control programming.
While the first 2D CAD programme created specifically for PCs was introduced by Autodesk in 1982, in 1994 AutoCAD R13 made the programme compatible with 3D drawing. A year later, Dassault Systèmes’ SolidWorks entered the market with the aim of making CAD more accessible to professionals. Today, these tools are taught in professional schools and adopted by all professionals because of the potential they offer.
CNC in Sinico
Since our beginnings at Sinico, we have adopted all the best technologies to equip our machines. With the rapid evolution of computers, we decided to enter into a close partnership with FANUC for the production of our CNC systems.
Thanks to this partnership, we have been able to achieve higher machining speed and precision. This, together with the optimisation of process steps, has enabled us to significantly reduce cycle times. In addition, we were able to expand our offer, giving our customer the possibility not only to have the motors and CNC systems but also to be able to integrate the modern robotic system.
See all our machines here or in action on our You Tube channel.