Metal working is the process by which the characteristics of a metal object are modified or altered through tools. Producing metal objects has improved man’s quality of life by allowing him to make light and durable objects such as: hunting weapons, cooking utensils, as well as ornaments and trinkets. Now this technology has evolved greatly and with the help of machines we are able to produce components found in many everyday objects including automobiles.
Metal working Techniques
In metal working we go about exploiting the physical characteristics of the material in question, looking for the optimal way to modify its shapes. There are various techniques that fall into two main categories:
- hot metal working;
- cold metal working.
The difference between the two methods does not refer to the absolute temperature level, but considers the relationship between the melting temperature of the metal in question and the temperature of the metal during processing.
Hot metal working
As mentioned above, the distinction is based on the value of the ratio, which in this case must be greater than 0.6. Within this subdivision we find:
- Forging: the metal here is heated to the point of malleability and then beaten with a mallet until it reaches the desired shape. Finally, the piece is cut and beveled or filed to perfect the corners;
- Casting: in this case the metal is brought to fusion and placed in a mold until it becomes solid again. The mold is then opened and the part is finished to chamfer the corners;
- Stamping: this process consists of blowing air into the chimney in which the metal is put until it turns bright red. After that it is struck with a sledgehammer to give it the desired shape.
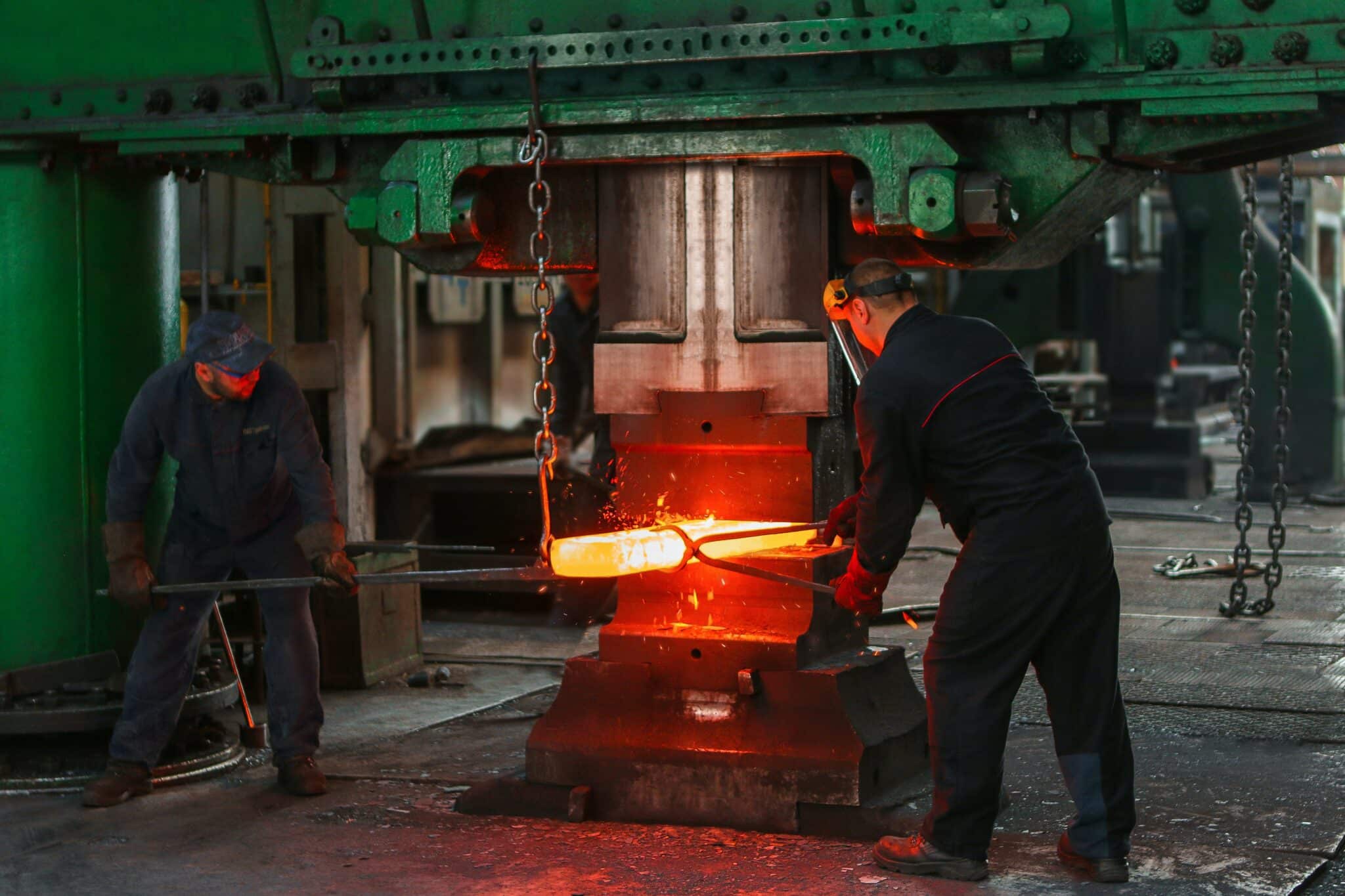
Cold metal working
In contrast, however, in “cold” machining the temperature of the metal remains such that it does not exceed 0.3. The main techniques that fall into this category are:
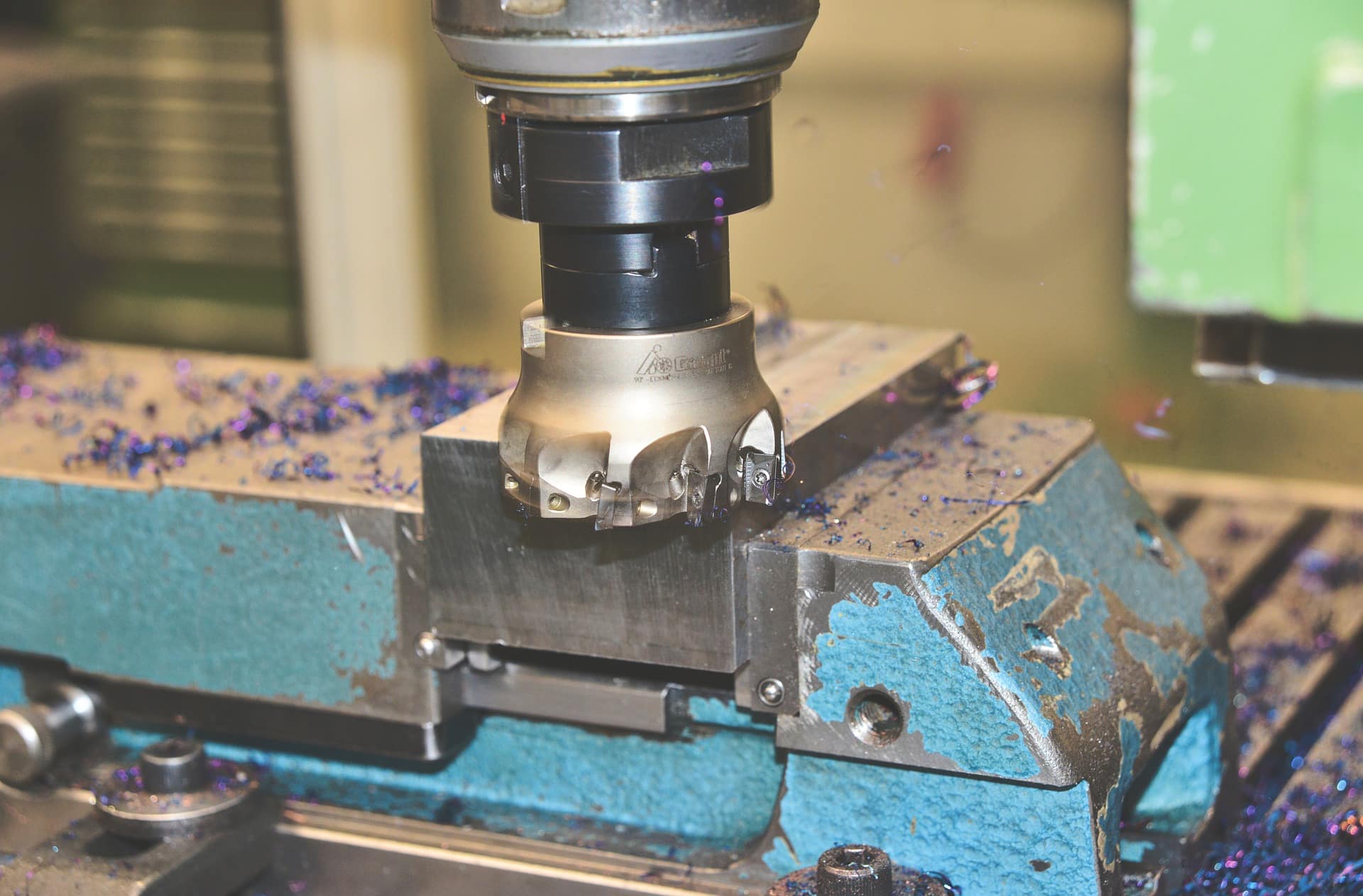
- Machining with chip removal: this technique involves the selective removal of excess material using a special tool in order to obtain the desired size and shape. Operations that fall under this technique include: turning, chamfering, facing, drilling, thread boring, reaming, forming, marking, milling, and grinding;
- Deep drawing: this operation makes it possible to transform a sheet metal into an object with a concave shape;
- Drawing: is used for the production of wire and involves pulling the material through a shaped hole, using a pliers;
- Rolling: is the mechanical process used to decrease the least significant dimension of a sheet of metal, usually the thickness;
- Bending: by it, an attempt is made to deform an object, thymically a sheet metal, by the application of an appropriate force;
- Extrusion: involves imparting an appropriate compressive force to force material through a shaped opening:
- Laser cutting: this type of cutting veins carried out by means of a laser beam that, when striking the surface of the material, heats it to the point of melting and vaporizing it. Once then the beam band completely penetrates the material, the actual cutting process begins;
- Shredding: this operation involves cutting into pieces, strips, or shredding matter.
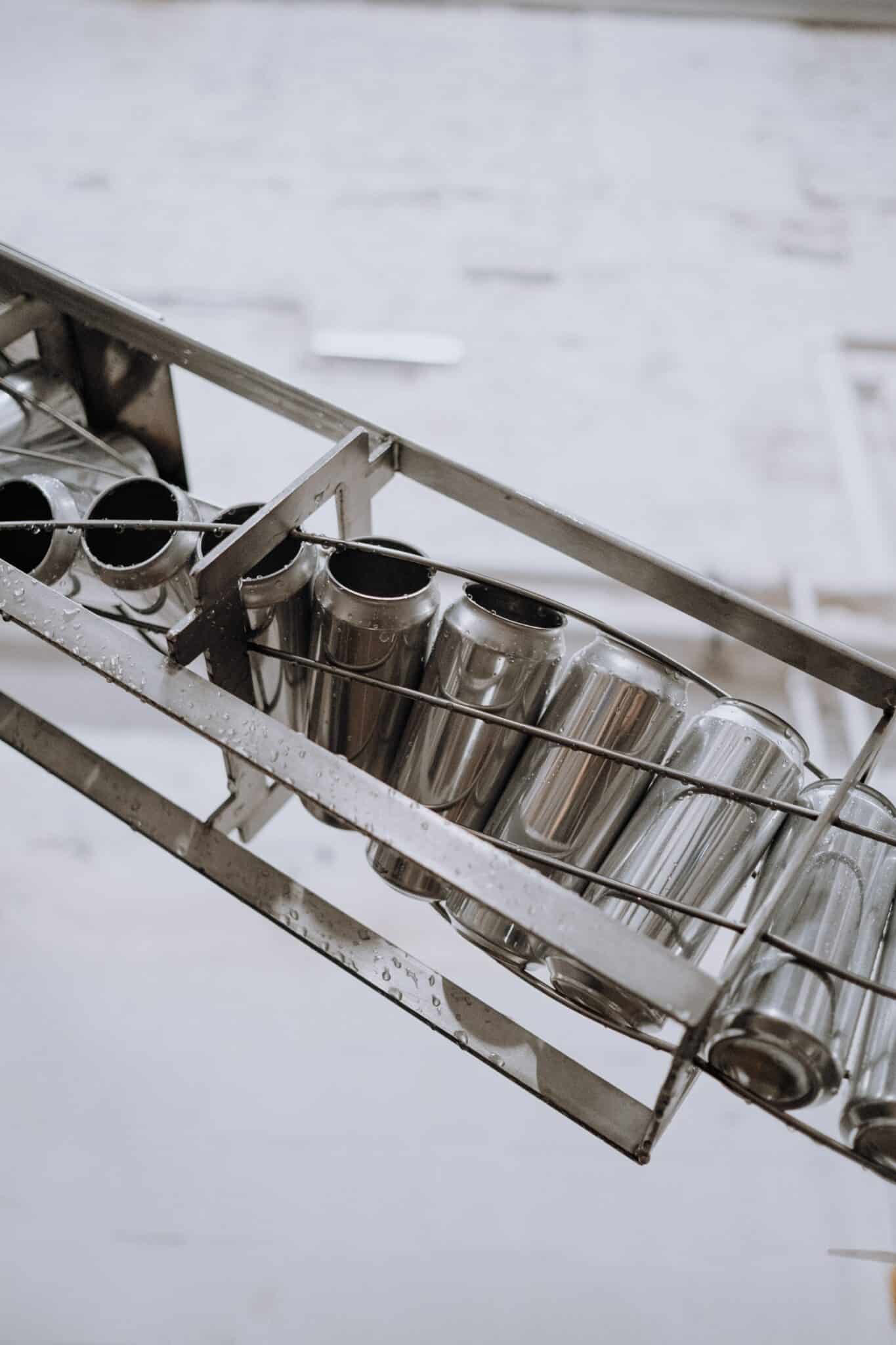
Metal working machinery
Special machinery is used for metalworking that can perform the operations with the necessary precision and speed. Usually each machine is designed to perform only one of the techniques described above. The main types of machine tools are:
- Lathe: for machining axisymmetric objects;
- Boring machine: for finishing the inner surface of hollow objects;
- Milling machine: for creating grooves;
- Choking machine: for making small grooves;
- Shaper: to obtain a smooth and flat surface;
- Planer: capable of obtaining a large flat surface;
- Grinding wheel: machine capable of grinding, cutting, grinding, deburring or sharpening.
CNC Transfer Machines for Metalworking
On many occasions, the finished product to be obtained has characteristics that make it necessary to work with more than one machine tool. For this reason, CNC transfer machines are born.
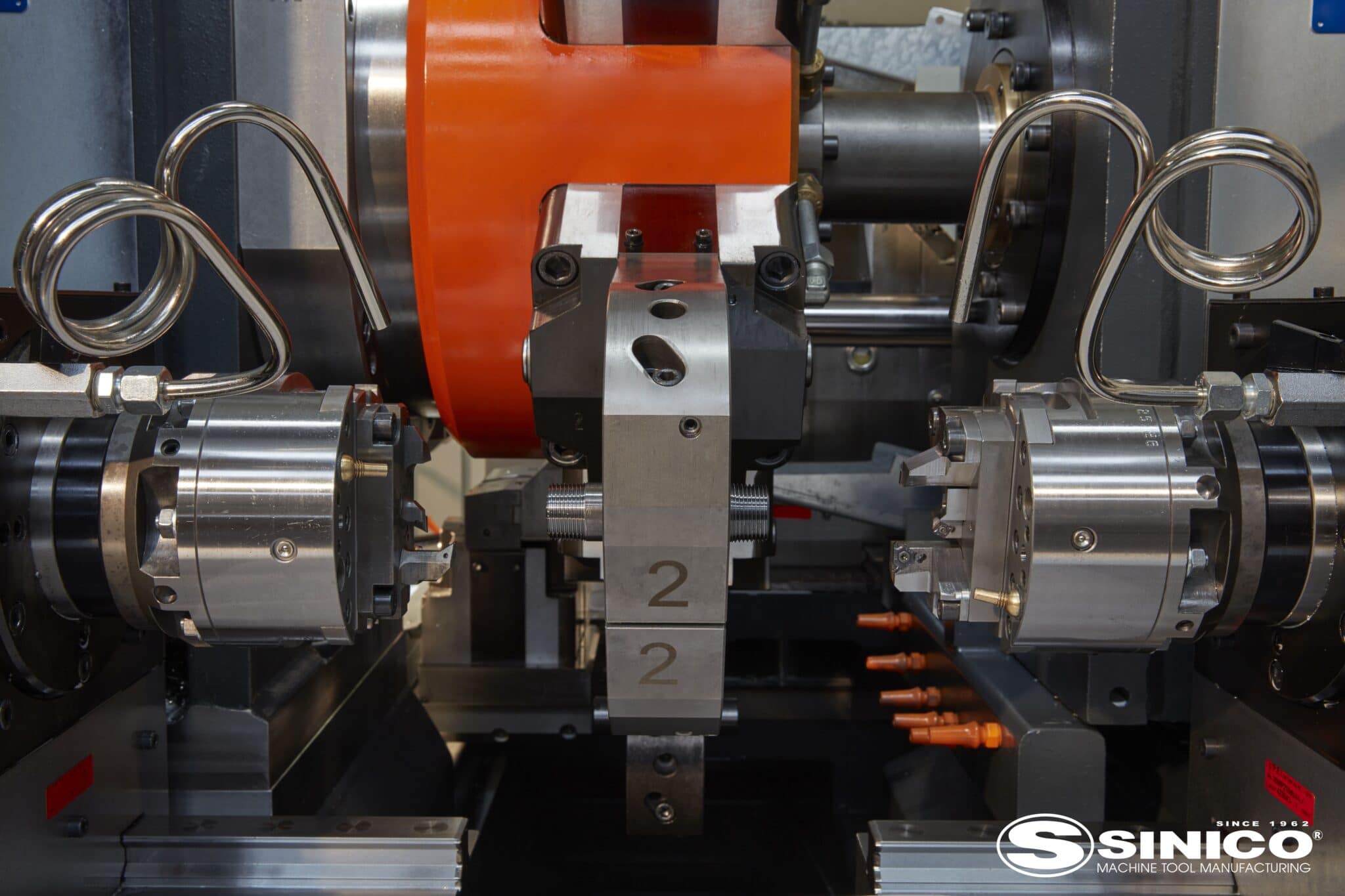
In this way, thanks to the possibility of equipping the machine with different types of tools, the various necessary operations are carried out smoothly, optimizing each stage of production.
The reasoning behind the operation of such production lines is that the processing and transport speed of the workpiece is higher if it is transported automatically to the various stations. Thus, thanks in part to the invaluable help of computerized numerical control, the processing of the metal product is precise and fast, thus achieving high production volumes, which are indispensable in many industries such as automotive.
Sinico Transfer Machines
At Sinico, we have been designing transfer machines specializing in cutting to length and machining at the ends of metal parts since 1962. Our three lines are capable of machining metal objects of widely varying sizes. In fact, thanks to them, small parts such as close nipples, bushings, and small fittings up to motor shafts, axial shafts, or construction micropiles can be made.
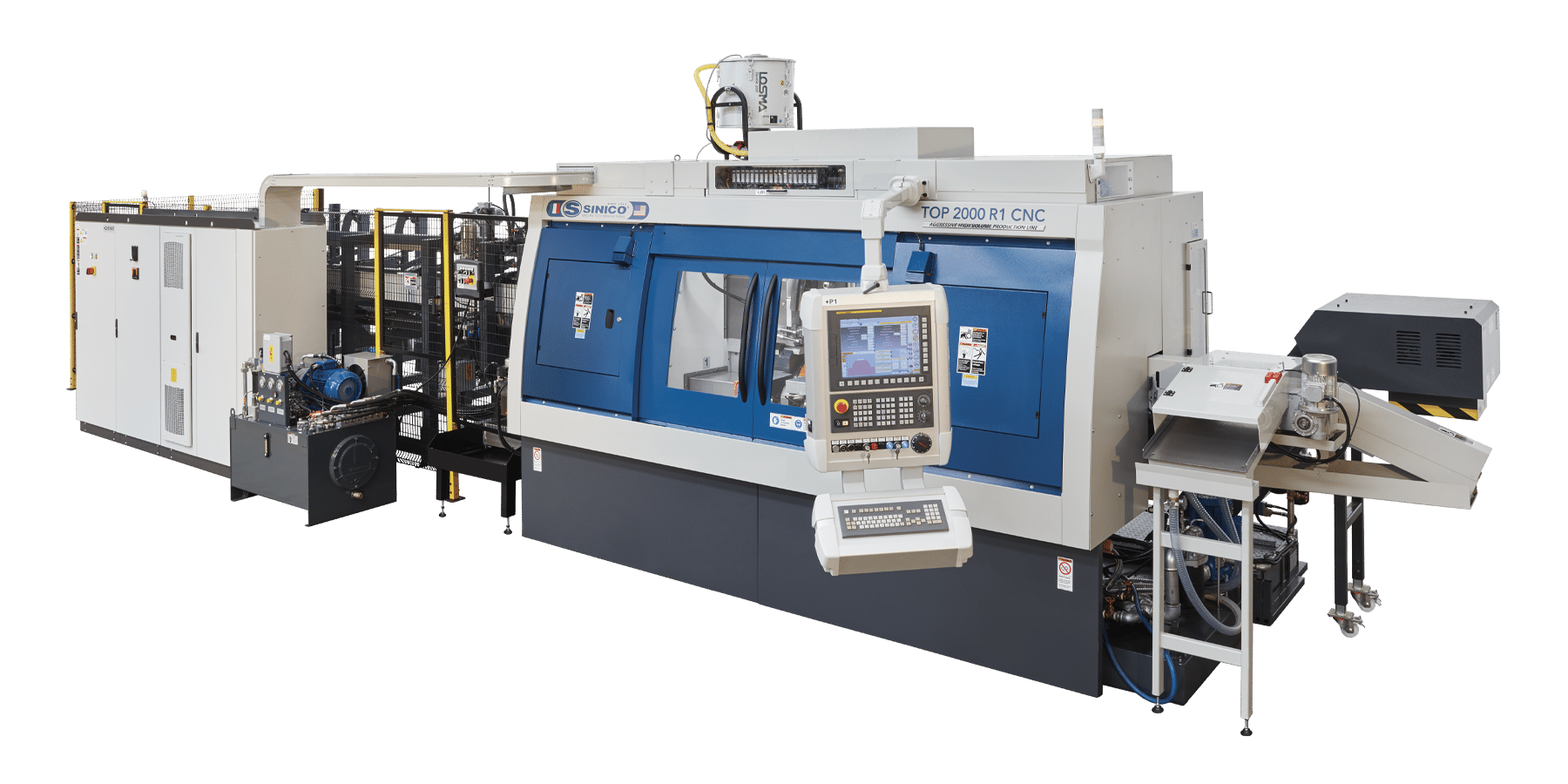