Boring and reaming are both operations by which the diameter of an existing hole is modified. These two operations are so similar that they are often used synonymously in common parlance. However, although their differences are minimal, they are substantial. Let us therefore analyse what distinguishes boring from reaming.
The Boring
As we have seen, boring is used to increase the size of an existing hole. Depending on the material and the objective to be achieved, the most suitable working method will be identified by choosing the speed and type of tool. This can be stepped, i.e. with the inserts arranged at different axial heights, ideal for roughing while maintaining better chip control. In the case of special materials that make stock removal difficult, single-edged blanks are used instead. Finally, tools with several cutting edges are used if there is a large amount of swarf to be removed.
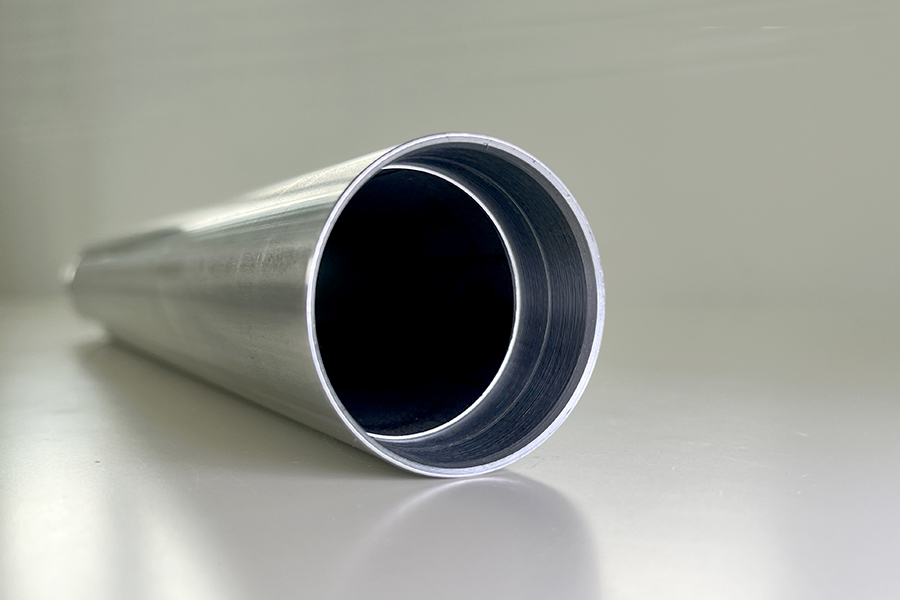
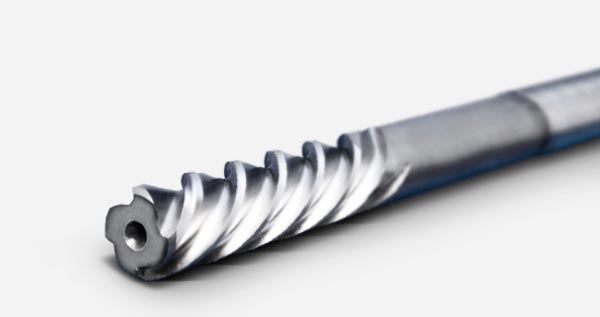
The Reaming
Reaming is the process in which material is removed from the surface of a hole in order to obtain extremely refined diameters and hole surfaces characterised by a quality that minimises the friction generated. In addition to this, reaming also has the function of correcting the axiality of the hole. In addition to this, reaming is also used to correct the axiality of the hole. In order to guarantee the quality of this particular machining operation, CNC machines are generally used, which are able to control each stage of the operation and ensure that the required tolerances are met.
Main differences between boring and reaming
The similarities are clear reading the given definitions given, but here are the main and most significant differences between the two machining operations:
- Purpose and level of precision: the purpose of boring is to roughen by increasing the diameter of a hole, while reaming is used to finish the surface of a hole. For this reason, the precision of the latter machining is higher;
- Type of tool: the tool used in boring has only one cutting edge while reamers are multi-cutting.
- Formed chip: since boring is a roughing operation and can also increase the diameter a lot, the swarf created is also larger. Reaming, on the other hand, only removes material from the surface of the bore;
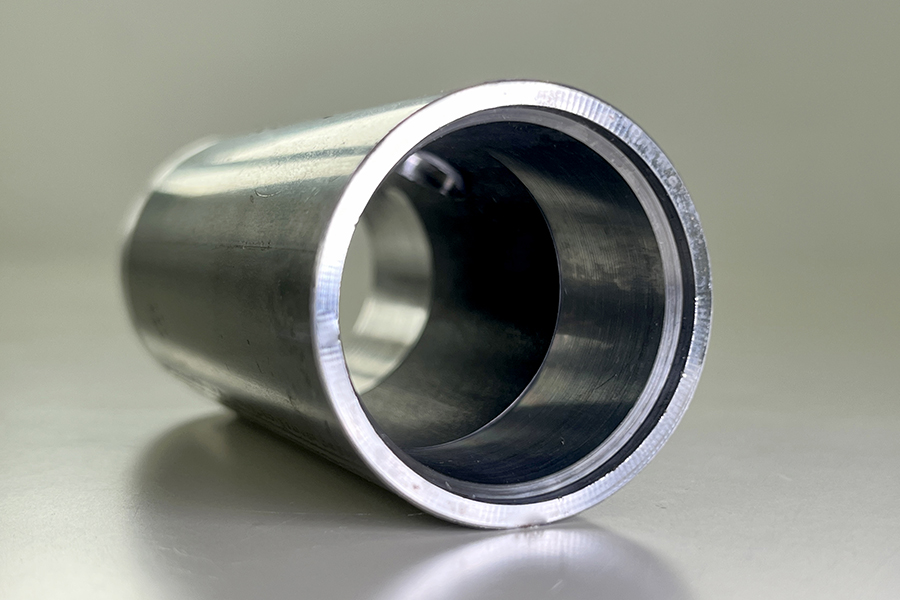
- Tool speed: In order to maintain high precision and not have a large amount of material to remove, the tool speed during boring is lower than during boring. Therefore, it goes without saying that the heat generated and the need for coolant is also lower;
- Tool movement: in boring, the tool movement is linear along the axis of the hole, while in reaming, the cutting edge rotates around the axis;
- Cost: Due to the higher accuracy of the operation, reaming costs more than boring at the level of individual machining.
These aspects are crucial if, due to available resources or technology, they are seen as alternative operations. In this case, the choice must be made on the basis of the characteristics and in particular the precision tolerance that the finished product must have.
In many processes, however, these two machining operations are complementary and both contribute to the production of a high-precision hole. This is possible with transfer machines like Sinico Top, which are designed to carry out several steps of a single working process with only product line. In them, boring and boring tools can be integrated into the work cycle, improving the quality and efficiency of production.