Boring is a machining operation whereby the diameter of a bore is increased by chip removing. The goal is to both enlarge and improve the quality of an existing hole in terms of finish, roughness and tolerance.
This is a so-called light finishing operation, as the material to be removed must be minimal and the hole on which it is to be applied must have a specific size. Boring is a necessary machining operation for the production of hydraulic cylinders, gears, bearings and other mechanical elements that require high precision in bores.
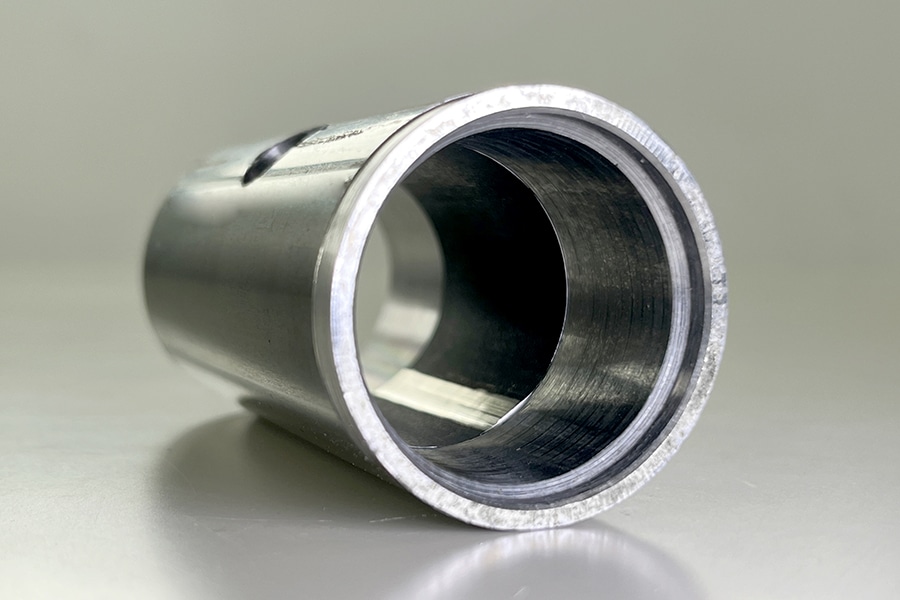
Main aspects of boring
Deep boring is a very common machining operation in precision mechanics. However, it presents difficulties that require special attention if an adequate level of precision is to be achieved. Among these are two of crucial importance:
- Tool selection;
- Tool speed;
- Management of the heat generated.
Tool selection
Cutting tools used in boring are made of steel, tungsten carbide or ceramic materials. They come in various shapes and sizes, depending on the requirements of the project, and are chosen according to factors such as the material to be cut, the diameter and depth of the hole, and the desired finish.
Different diameter ranges are therefore used depending on the need:
- For roughing, tools from 25 to 500 mm are used;
- For precision boring, tool diameters from 3 to 981.6 mm are used;
- For reaming, diameters from 10 to 31.75 mm are used.
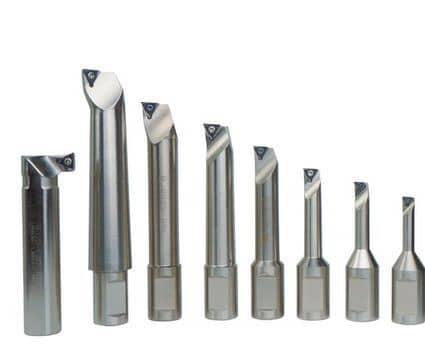
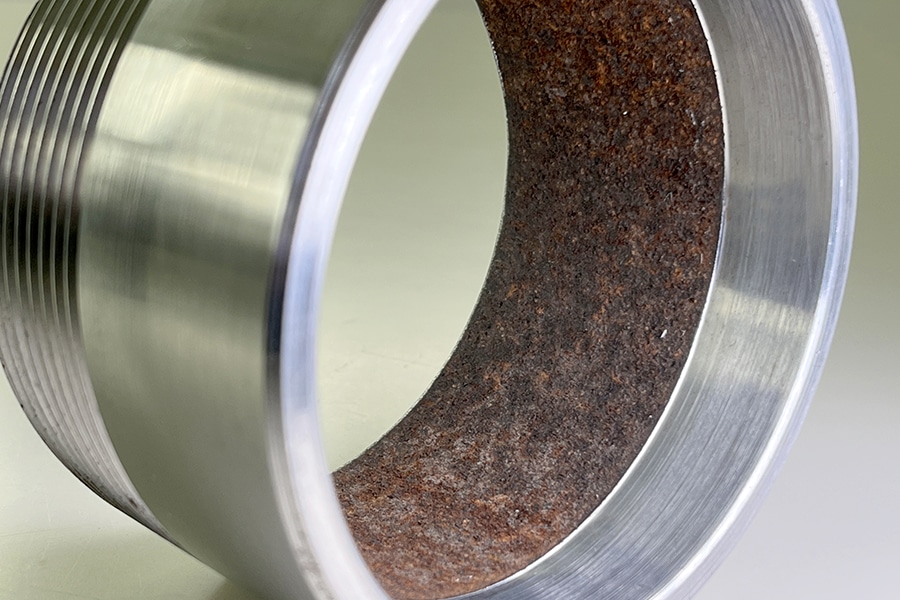
A further aspect influencing tool selection is the amount of chip created during machining. It is directly related to the type of workpiece material and the increase in diameter of the hole to be machined. These boring heads are generally used:
- Single-edged heads: used for finishing or roughing on materials where removal is difficult;
- Multi-edged heads: Used where there is a lot of swarf to be removed. Therefore the performance is guaranteed due to the fast feed per tooth.
- Stepped heads: These tools have clutches set at different diameters and axial heights. This allows better chip management.
Tool speed
The speed of metal reaming can be a determining factor, depending on the application and specific requirements. Factors that can influence speed include the type of material, the size and complexity of the hole, the type of boring tool used and the specific requirements of the project.
In some cases, a higher boring speed may be desirable to increase productivity and efficiency in the face of increased tool wear. While in other cases, a lower speed may be necessary precisely to ensure accuracy and precision.
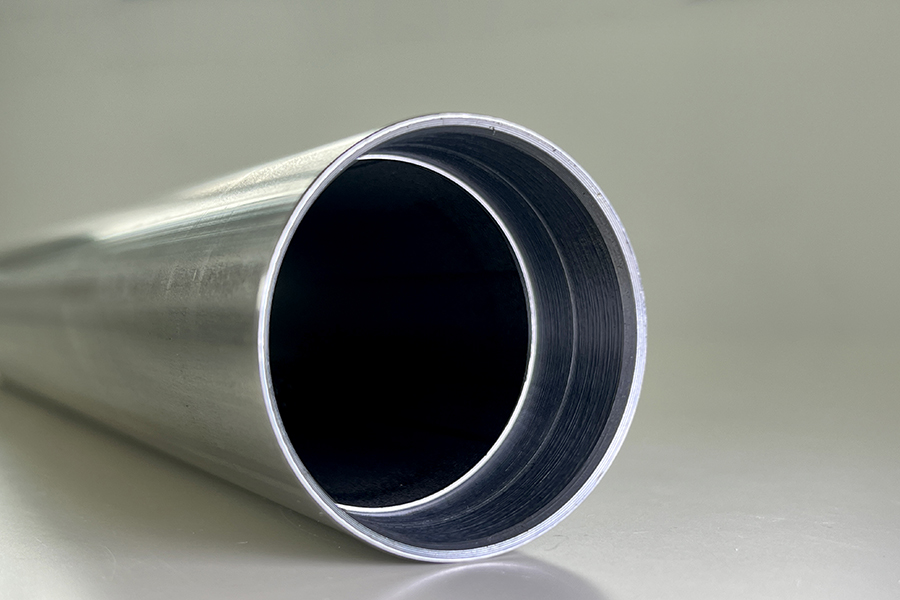
Management of generated heat
One of the challenges of boring is managing the heat generated during the process. This can cause the workpiece to expand, compromising the accuracy of the hole created. The main problems are:
- Tool wear: excessive heat generated during metal boring can cause rapid wear of the cutting tool, reducing its service life and increasing replacement costs.
- Workpiece deformation: deformation of the workpiece can occur, resulting in inaccuracies and surface defects in the final product.
- Reduced cutting speed: if the heat generated during reaming is not controlled, it can reduce the cutting speed of the tool, slowing down the entire machining process and increasing production time.
- Surface finish problems: the surface of the workpiece may be rough or uneven, resulting in a poor surface finish.
- Thermal breakage: In extreme cases, the heat generated can cause thermal breakage or other damage to the workpiece, rendering it unusable
To mitigate these problems, various cooling methods are used during metal boring, including cutting fluids, air or oil mist and cooling systems, which help to reduce the temperature of the cutting zone and improve machining performance.
CNC machines for boring
When it comes to metal boring there are many aspects to consider, but at the same time precision and repeatability are key factors. The slightest error can result in added costs, wasted materials and compromised products. For this reason, especially in the case of high production volumes, CNC machines capable of programming and controlling the machining process are used.
Sinico’s production lines are a perfect example of this type of machinery. Our experience and choice of the best components allow us to meet the challenges and problems mentioned above, always providing the solution to optimise production with the lowest possible cycle time.
If you are interested, visit our You Tube channel to see our machines at work.